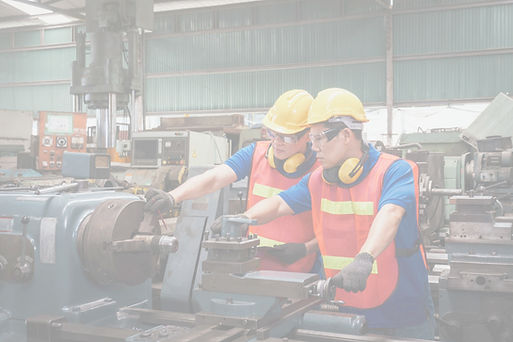
Valve Services
Achieve Operational Excellence with
Brand Agnostic Solutions with excel valves
Excel Valve Services offer a comprehensive range of on-site or off-site valve upgrading, reconditioning, repair, modification and overhaul programmers which are impartial and independent of the restrictions imposed by manufacturers and their agents. Excel Valves Services has the capability to complete all repair workshops in house, we are a one stop shop for all valve service requirements. From a custom built facility enabling fast and efficient processing of work to understand different valve failures through engineering. This all leads to improvement, reliability and longer service life for any valve type, size and rating.
We use the latest technology and techniques to identify and repair any issues, and our highly experienced technicians are available 24/7 to provide you with the best service possible. We guarantee a quick turnaround time and competitive prices on all our services.
Excel Valves Services has access to over 500+ trained valve engineers, design engineers and metallurgists, allowing the service of every type, size and class of valve including:
The range of valve field services provide by Excel Valves include:
Evaluation to prevent potential valve problems occurring
Troubleshooting and routine valve maintenance including flushing & lubricating
Condition Monitoring
Rebuilding
Freeing of seized or hard to turn valves
Emergency Valve Sealing
Commissioning of newly installed valves
Verification of valve integrity
Valve leak detection by acoustic monitoring
In-line overhaul Safety
The proper functioning of valves, including emergency shutdown valves on both onshore and offshore oil and gas installations, is essential in ensuring the safety of personnel, protecting the environment and safeguarding capital assets. Thanks to EV'ss tringent Quality Control System, the safety standards which we achieve for all aspects of our Valve Services more than meet the relevant Government legislation requirements.
Flange conversions
-
Convert Flanged End Valves to Butt Weld End
-
Convert Raised Face Flanges to Ring Type Joint
Installation of special packing and gaskets
-
Mounting a full range of valve actuators, from gear operators to sophisticated
-
motor,
-
pneumatic, hydraulic, and electric actuators
-
Special Cleaning
-
Install By-Pass valves
-
Valve Testing
-
PMI / Positive Material Identification
-
Testing
-
NACE Trim parts
-
Special Ball Materials
-
Cryogenic Columns
-
Stem Extensions
-
High Head Extensions
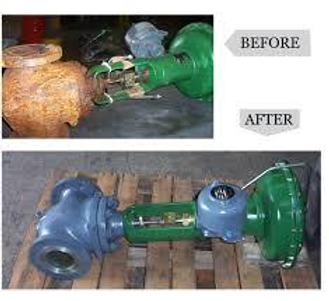

Procedure for Servicing, Testing and Installation of used pipe line valves which are leaking.
Visual Inspection:
The leaked valve which comes for reconditioning shell under for initially visual inspection which calls for identify and rectify the surface defects, Scratches and fittings on surfaces due to atmospheric corrosion or due to process effects
(I.e. Due to the leakage of medium through gland and failing on the outside surface
of valve)
No surface defect, fitting should be left out without attending for repairs and rectification. This should do as per the Standard MSS-55 which covers the quality of steel casting under visual methods.
No corroded surface / component should be left on valves and it should Identified and replace with new / reconditioned on so as to ensure the life of the replaced component which should not affect the life of the valve. All defective component shall identified with reliable marks like paint etc., and should sent for further inspection.
Dismantling of valves:
The leaked valve which under goes reconditioning shall be dismantled and every component will be identified with marks so as to enable inspection / assembly department to take cares about components for further process.
While dismantling the valves gland packing Gasket, and Bolt / Nuts are to be separately identified which are to be replaced with new. No reconditioned / repaired Gaskets, Bolts / Nuts and gland packing will be used in assembly.
All dismantled components like Stem, Wedge/Disc, Ball, Seat Rings, back seat bush (if applicable and other item) are to be cleaned with kerosene or acid before sending in to inspection.
Inspection of components of after dismantling:
All components like Body, Bonnet, Cover, Stem Wedge / Disc / Ball, Sealing etc., are to be inspected completely before passing to production department. The defective components are identified and will be rejected (if it is not possible to repair) No components shall be passed as it is to production without prior inspection and report.
Reconditioning of Components and internal valve parts:
Body:
After Inspection, if any defect has noted on body surface of on flange face or the cover face if should be re-machined / ground with respect to the complexity of the defect. After all repair, the body should be thoroughly cleaned.
Bonnet/cover :
In bonnet of first the back sealing area is thoroughly inspected for any scratches or corrosion due to the flow medium. If any defect has noted on back seat bush it should be replaced with new to suit the bonnet and stem. If any scratches noted on back seating surfacing of the bonnet it should be machined so as to get a defect free back seating face to avoid back seat leakage while replacing the packing.
Seat Rings:
Before dismantling, the valve has to be hydraulically tested (High pressure test) identify the leakage of seat, seat rings. The leaking area to be marked with paint. Seal rings are to be removed if it is threaded type or to be machined and removed if it is seal welded type. New seat rings to suit the body to be machined, hard faced and finished so as to suit the wedge accordingly to get leak tightness at the minimum closure torque. Seat rings must undergo hardness checking, liquid penetrant checking in order to ensure required hardness as per relevant standard and crack free respectively before finishing for final assembly. Seat rings will be lapped properly to get fine finish.
Wedge/ Disc:
After dismantling will cleaned with kerosene or Acetone and then Inspection thoroughly for any defects like erosion. Abrasion or corrosion due to medium or scratches on seating face due to improper closing or opening of valves while
operation if any defect noted on the wedge/disc it will be repaired. The seating faces of the wedge/disc are to be hard faced with the material and will be lapped to suit the body seat faces.
Stem:
This is one of the main components in valve which transmit the motion from hand wheel to wedge/disc for opening and closing the valve against line pressure. This may have got corroded, pitting might have occurred due to the medium it will be thoroughly inspected and if it is not possible to repair, should be replaced with new
with required hardness as per relevant standards.
Replaceable Components:
Gland Packing:
This will be replaced to provide leak tightness at the gland.
Gasket:
This provides leak tightness at the body/bonnet joint. This must be changed with new one. The same gasket could not be used.
Back Seast Bush:
This combine with stem to provide back seal for the valve. If necessary it should be replaced as per customers’ requirements.
Bolting:
All body/bonnet boiling will be replaced with new bolls/nuts as per relevant standard or as per customers’ requirements.
Blue Matching means matching the sealing faces of seal and wedge/disc to ensure leak tightness while testing and application. After assembly of body seat rings and the sub-assembly of bonnet, the seating faces of wedge / disc should be applied with blue and the valve shall be closed with to torque and successively shall be opened
to see the matching of seat ring and wedge / disc seating aces.
Assembly:
After thorough blue matching valve shall be assembled with a new gasket, gland packing, bolts/nuts and it will be subjected to Hydraulic and pneumatic testing.
Pressure Testing:
To assure functional quality, valves need undergo pressure testing. This can be
described as routine test. Routine tests for valves are:
1. Hydraulic pressure test
2. Seal leakage test
3. Gland leakage test
Pressure testing shall be performed on recondition valve as per the standard referred in references. The test pressures for the hydraulic and pneumatic test are given. The test duration in minutes (minimum) for the above tests is as per the standard API 598 & BS 6755 part-1
After the completion of testing if the valve passes through all tests and meets all requirements as per the above referred standard, will be taken for painting. Aluminium paint is to be painted on Carbon steel. Alloy steel valves. No painting is required for stainless steel valves. All areas are to be painted except stem which cause operational problems like scoring of stem and gland packing and easy closure and opening of valve.
INSTALLATION:
After completion of inspection at the customers end the valve will be installed by
us (if required) on the pipe line




Pressure testing Unsurpassed for Accuracy, Reliability and Safety with excelvalves
+91 8531066857
